Carbon autoclave (also called composite autoclave) system is specially designed for composite materials production, it is very important to develop software to control completely control of the internal temperature, pressure and vacuum according to the composite material technical requirements. The resin reaction process is the main composite material curing process, therefore, the development requirements of composite curing process include the curing of the resin properties, the thermal properties of mold, product accuracy requirement, layer design and other complex technological factors. With the addition of these technological factors, the control ability of carbon autoclave equipment is highly required.
Meanwhile, with the spread of the application range of composite materials, the output is increasing, and the cost requirements are constantly reduced, the control functions of the equipment should be optimized to control when multiple products are imported at the same time. The reasonable control method should be realized to improve the energy conservation and reduce the cost at the same time.
At present, the development of composite technology is very fast, the curing characteristics of the resin is more and more optimized, for small size, low requirements of composite components, with the promotion of “beginning pressure” resin, process simplification, the requirements for carbon autoclave control system is reduced. However, for the larger size, more complex and special functional resins and other high-end fields require a strong control function to achieve the process objectives. For mass production of composite components, curing processes are the key to control the quality stability of composite component processes to ensure that every batch production in the same curing condition to finish curing. In order to ensure the quality consistency, the automation level of the software for the control of the carbon autoclave puts forward high request, “no human intervention” realizes full automation, the same process consistency is important in the cases of the control function of requirements.
In conclusion, the main control parameters of the carbon autoclave system are temperature, pressure and vacuum. However, in combination with the technological characteristics of composite materials, especially to realize the automation of the curing process of composite materials, the functional requirements of control software are very high, and the group of software development technicians should have a deeper understanding of the technological characteristics of composite materials and curing processes.
STRENGTH Equipments also has the manufacturing ability and the composite material product development ability, in order to provide users with better equipment, help users to achieve high-end product production, after long-term efforts, developed a set of carbon autoclave system special control system and software.
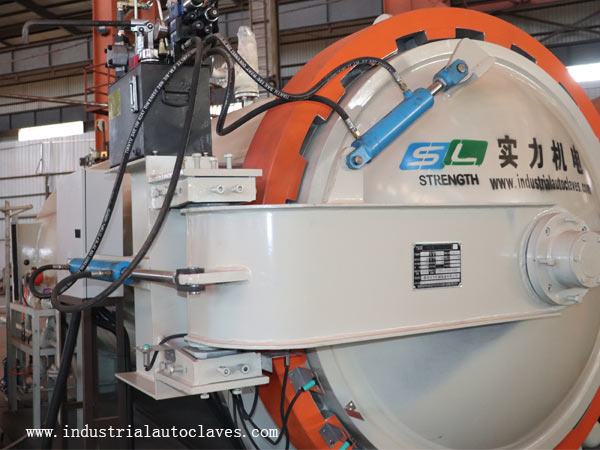
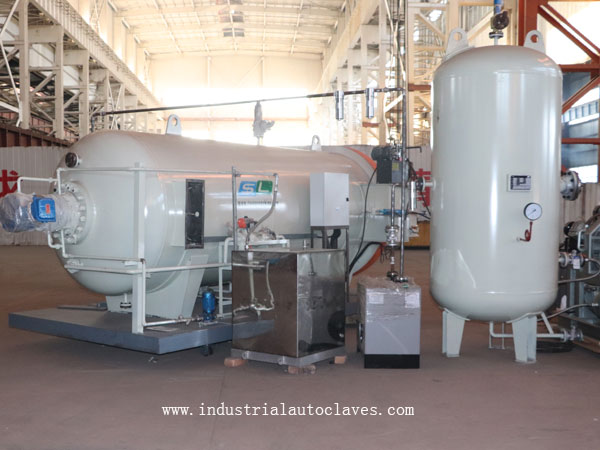
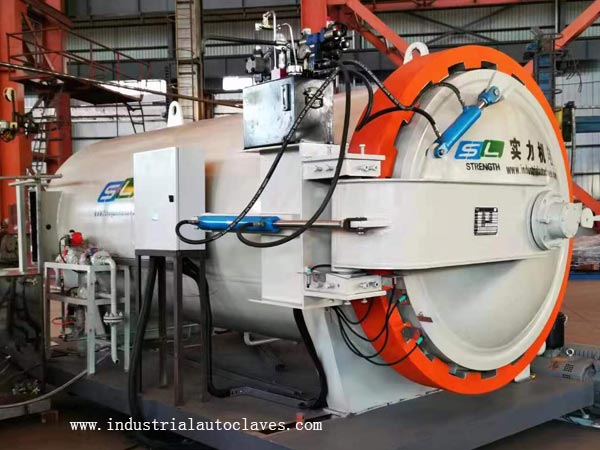
1. Control Structure
The control system is based on bus-based hardware design. The main controller adopts Siemens controller, industrial bus communication, strong anti-interference ability, large amount of data. The upper computer adopts industrial control computer and software monitoring, which can display the alarm, report and record the temperature rise curve in real time, and monitor the running status of the equipment.
①Adopt dual core working mode. The computer analyzes the process and reads the process in advance to make and judge the future temperature and pressure changes. The PLC executes the instructions of the upper computer, performs real-time comparison operation between the target value and the actual measurement value, and adjusts the output signals of temperature and pressure.
②Implement redundant control. In order to ensure that the production will not be affected in the case of PLC failure, the manual redundancy control is added, and the intelligent instrument redundancy control can be added.When intelligent instrument redundancy control is adopted, the upper computer sends instructions completely, and the instrument control and PLC automatic control can achieve seamless connection.
③Modular installation ideas.The thermocouple and vacuum signals are collected by modularization and sent to the upper computer by the communication module, which greatly reduces the wiring and interference and simplifies the difficulty of installation and maintenance.
2. Main Interface Description
The upper computer interface is divided into monitoring interface, operation interface, maintenance interface, warning interface and other four interfaces. In order to prevent the wrong operation, according to the different permissions, the operation mode of different interface open different permissions.
About STRENGTH Equipments
Taian STRENGTH Equipments Co., Ltd is the professional pressure vessel designer, manufacturer and exporter dedicated in supplying finest quality industrial autoclave, storage tank and dish head products and solutions to worldwide customer over 20 years. We have over 80 talented research and development experts, 2 million square meters manufacturing factory and more than 50 sets large-scale manufacturing machines. Our annual industrial autoclave and storage tank output can reach over 300 sets, dished head output can reach over 3000 sets.
STRENGTH Equipments is not only manufacturing high quality industrial autoclaves, storage tanks and dished ends but also providing custom product design, fabrication and after-sale service. ODM, OEM are also available. If you have any questions or inquiries, please fill and submit the following form, we will reply as soon as possible.